Today we are looking at Proteus circuit design. Whether you are new to Proteus PCB design, or in need of a refresher, this informative article attempts to explain the process in as straightforward a manner as possible.
Contents
How to Print PCB Layout from Proteus
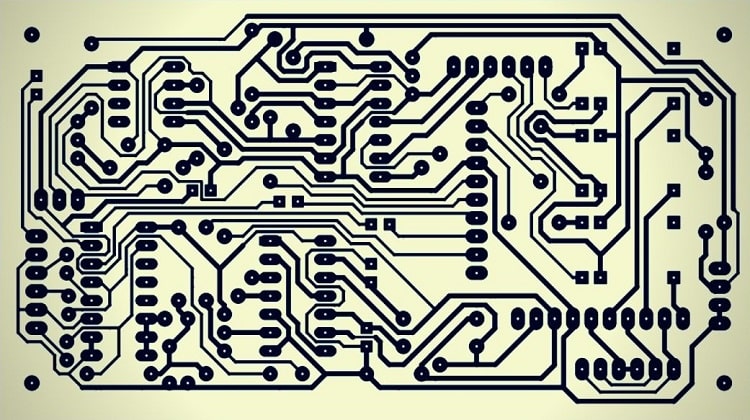
A. WHAT IS A PCB?
PCB stands for Printed Circuit Boards. If you are familiar with electronics, you will know that these components are frequently used.
A PCB is made up of a base material (a copper plate), a substrate, and other components that are usually fixed to the circuit using solder.
B. TYPES OF PCB
1. DOTTED PCB
This type of PCB has dots on its surface. The holes on the surface are where components get inserted. These components then get wires attached to them which get soldered together.
Dotted PCBs are difficult to design and often lead to a lot of errors.
2. LAYOUT PCB
Layout PCBs are much more simple. The layout is created using PCB design software. This design is then etched onto a copper plate, followed by components being soldered onto the board.
This method results in fewer errors and is also less time-consuming to make.
C. PROTEUS
There are many different software available for PCB design. However, the focus of this article is Proteus.
Proteus is rich with tools that are easy to use and provide great assistance in designing PCBs. Even if you are new to PCB design, you will find Proteus helpful as you learn.
Features that Proteus boasts are:
- 3D viewing
- An integrated auto-router
- Configurable design rules
- Full schematic capture
- Interactive circuit simulator
- Support for power planes
D. STEP-BY-STEP GUIDE TO PRINTING PCB LAYOUTS FROM PROTEUS
STEP 1: DESIGN YOUR CIRCUIT
Start by running the program.
Once the program is loaded, you should see your workspace with all the tools at your disposal at the top and running down the left-hand side. In the middle is a blue rectangle. Within this blue rectangle, the circuit will be designed.
STEP 2: SELECT COMPONENTS
The components you will use depend on the type of circuit being designed, so we won't go into how to select specific components right now.
However, to access the components you can choose from, there are two ways.
- Go to 'Library' followed by 'device/symbol'. Components to select will appear in a new window.
- Use the toolbar on the left-hand side. Click 'Component model' or choose from the component library.
The components you have selected will be added to the devices list. These devices can be rotated. There are rotate buttons to do this.
When ready, you can start putting components into the workspace. Once all are placed, you can use the cursor to draw connections between the components, creating your circuit.
Should any component require a modification, right-click on it, and you will get a dropdown menu with modification options.
Once your virtual circuit is complete, save the file, and debug it.
STEP 3: DESIGN PCB LAYOUT - OPENING ARES
In this step, the virtual circuit will be used to design the PCB layout.
Proteus comes with the ARES designing suit integrated within it. This will be used as we design the PCB. To access ARES, open Proteus, click 'Tools', followed by 'netlist to Ares'.
You should see a window with a list of components.
To create the board edge, go to '2D Graphics Box Mode'>Select Layer>Board Edge.
You can now draw a box in the workspace. Once the box is drawn, click, and the line (green) will become yellow. Inside this yellow-lined box, the circuit will be drawn.
Remember, the box size is not limited to your initial drawing. It can be expanded if needed.
STEP 4: DESIGN PCB LAYOUT - COMPONENTS
Click on the components you want to use, using the rotate buttons if a rotate is needed, and then drag them to the workspace.
Once you have put all your components in the workspace, arrange them as required. Do this using 'selection mode'.
With all components in place, connect them. Use 'track mode' to change the width of the tracks. The width of the track depends on your own unique PCB design.
To connect components, click on the component end. A green line will appear, and you can drag this to the next component. Once done, the green line will disappear.
PCB Layers
- Single Layer
You will see the components on one side and connections on the other side.
- Double Layer
Both components and tracking will be seen on two sides.
- Multi-Layer
Each layer is shown as a different color: E.g., Bottom layer - blue, top layer - red, inner layer 1 - purple, etc.
STEP 5: DESIGN PCB LAYOUT - TRACKING
- White arrows show the direction of component traces.
- Green lines show connections
- Blue lines show track
- Red circles highlight tracking errors
Errors can be avoided by changing the track path.
If your PCB has more than one layer, you can change the track between each layer with the left mouse button. Double click this.
Remember, you can use the auto-router. This will let you set design rules and PCB width before it starts automatic routing.
Once tracking is complete, save the PCB project to the same file as your Proteus virtual circuit. You will be able to see a 3D visualization if you wish.
STEP 6: PRINTING THE LAYOUT
Go to 'Output'. Select 'Print'.
You should see a print layout window.
Select 'Artwork Mode' to print the yellow color module. Click 'Mirror' in the 'Reflection' section.
Print Options Explained
- Top Copper Layer
Used for dual-layer PCBs.
2. Bottom Copper Layer
Keep the scale at 100%. Click 'Mirror' in 'Reflection, and 'X Horizontal' in rotation. We select the mirror option because the side being printed will face the copper plate.
3. Top Silk Layer
You'll print this in addition to a bottom copper layer. This option will print the view of your components. For this, in 'Reflection', select 'Normal'.
4. Bottom Silk Layer
Used for dual-layer PCBs.
5. Solder Resist Layer
This option helps prevent short circuits. Use solder Resist>Bottom Resist>Board Edge. In 'Reflection' select 'Mirror'.
6. SMT Mode
This doesn't get used as an SMT module is not required.
7. Drill Plot Layer
Use to make prints for the drill place and hole size. In 'reflection', select 'normal'.
STEP 7: ETCHING
- Take your copper board and cut it to size.
- Place your print (glossy paper) on the copper board with the print facing the copper layer. Ensure alignment and secure everything in place.
- Use an iron or another heat source to apply heat for 5 to 15 minutes. This will cause the print to transfer to the copper plate.
- Once the copper plate and the print have combined, place the copper plate into lukewarm water. Remove the excess paper.
- Place the copper plate in ferric chloride solution. This will cause any excess copper to dissolve away, leaving only your design under the transferred print.
- Rinse the board.
- Remove the print using a thinner such as nail varnish remover.
- Sand down any rough edges.
- Drill necessary holes with a PCB drill.
- Place components and solder then.
- Cut extra pin.
And now your PCB is complete!